Introduction
Pump priming is a critical step in ensuring the effective operation of pumps, particularly centrifugal pumps, which require this process before they can begin functioning correctly. Essentially, pump priming involves removing air from the pump and suction line by filling the pump with the liquid that needs to be pumped. This process forces all the air, gas, or vapor contained within the passageways to escape, creating a low-pressure zone at the pump’s impeller eye. The atmospheric pressure, being higher than the created low-pressure zone, pushes the liquid through the piping, allowing the pump to operate as designed.
Without proper pump priming, air can get trapped in the pump, preventing the formation of sufficient suction to lift the liquid into the pump. When this happens, the pump is said to be “air-locked” and unable to function. In severe cases, running a pump without priming—referred to as “dry running”—can cause serious damage to the pump’s internal components, leading to costly repairs and downtime. This makes pump priming not only a routine part of pump operation but a critical safeguard for ensuring long-term performance.
- Introduction
- Quiz on Pump Priming
- Importance of Pump Priming
- Types of Pumps That Require Priming
- Check out Video on Pump Priming: Click here
- How to Prime a Pump
- Quiz on Consequences of Improper Pump Priming
- Consequences of Improper Priming
- Step-by-Step Guide to Manual Pump Priming
- Pump Priming Methods at a Glance
- Common Mistakes in Pump Priming
- Pump Priming in Different Industries
- FAQs About Pump Priming
Quiz on Pump Priming
1. What is one of the key reasons for priming a pump?
Choose the correct answer:
Correct Answer: B) To prevent airlock.
Explanation: Priming ensures that no air remains in the pump system, preventing airlock, which can stop the pump from functioning. For example, in a centrifugal pump, air pockets can cause the pump to lose suction and fail to operate efficiently.
2. How does proper pump priming impact maintenance costs?
Choose the correct answer:
Correct Answer: B) It reduces the risk of pump damage, lowering maintenance costs.
Explanation: Proper pump priming prevents dry running, reducing the risk of damage and costly repairs. For instance, an unprimed pump running dry can overheat and cause parts like seals to wear out quickly, increasing maintenance costs.
3. What is the role of pump priming in system reliability?
Choose the correct answer:
Correct Answer: B) It minimizes the chances of operational failure.
Explanation: Priming is essential for ensuring system reliability by preventing air from entering the system. A well-primed pump is less likely to fail during operation, making the system more dependable. For example, in a firefighting pump system, proper priming is critical to ensure that the pump works immediately in case of an emergency.
4. Why is pump priming essential for the pump’s long-term durability?
Choose the correct answer:
Correct Answer: B) It minimizes wear and tear caused by dry running or air-induced cavitation.
Explanation: Priming prevents dry running, which can cause friction and heat build-up in the pump, leading to significant wear and tear. For example, cavitation (air bubbles collapsing inside the pump) can cause pitting on metal surfaces, reducing the pump’s lifespan.
5. How does pump priming contribute to improving pump efficiency?
Choose the correct answer:
Correct Answer: A) It ensures the pump is fully prepared to handle liquid flow without unnecessary strain.
Explanation: Priming clears air from the system, allowing the pump to operate smoothly and efficiently. For example, in irrigation systems, a well-primed pump ensures consistent water flow with minimal energy waste.
Complete Course on Piping Engineering
Basics, Codes & Standards, Layout, Materials & Stress Analysis
Importance of Pump Priming
Priming is not just a step but a crucial element in the successful operation of various types of pumps. Let’s dive deeper into why it’s so essential:
- Prevents Airlock: Priming ensures that no air remains in the pump system, thus avoiding the risk of an airlock, which can stop the pump from functioning.
- Improves Efficiency: A well-primed pump operates more efficiently, as it is fully prepared to handle the liquid, avoiding unnecessary strain.
- Reduces Maintenance Costs: Proper pump priming reduces the risk of damage from dry running, which in turn decreases maintenance costs.
- Ensures Long-Term Durability: Regular priming helps extend the life of the pump by minimizing wear and tear caused by dry running or air-induced cavitation.
- Enhances System Reliability: With regular priming, pump systems are less likely to experience operational failure, increasing their reliability.
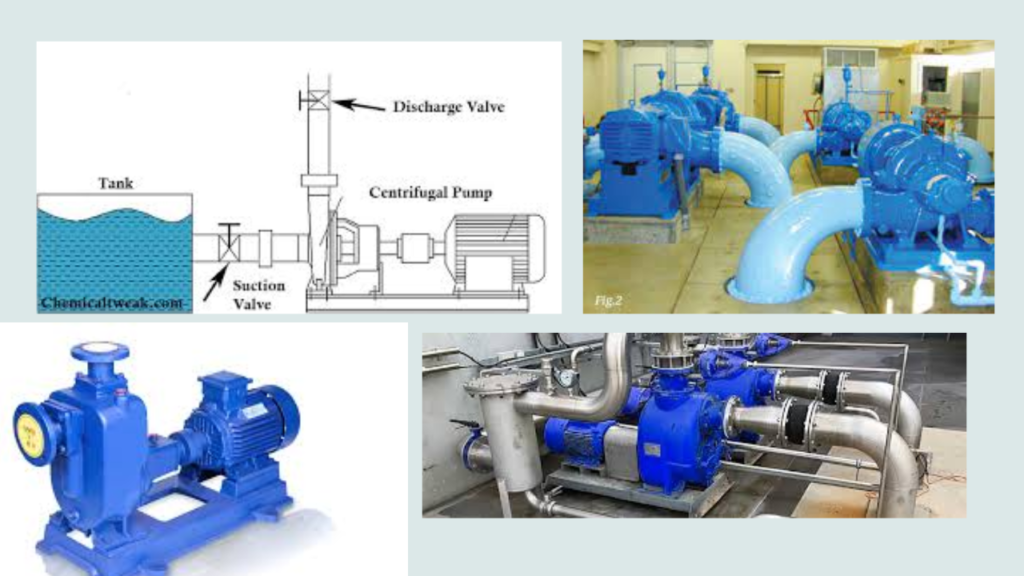
Types of Pumps That Require Priming
Not all pumps need to be primed. Let’s break down which types require priming and which do not.
Centrifugal Pumps
Centrifugal pumps, which rely on the centrifugal force to move liquid, must be primed after each shutdown to eliminate any air that might have entered the pump. If air gets trapped, the pump will lose suction power and will not function as expected.
Positive Displacement Pumps
Positive displacement pumps also require initial priming, but once primed, they typically maintain their priming state unless the system is opened or drained. These pumps operate by trapping a fixed amount of liquid and then forcing it through the discharge pipe.
Self-Priming Pumps
Some pumps are designed to be “self-priming.” These pumps can create a vacuum internally, enabling them to automatically prime themselves when required. However, they still need to be manually primed before their first operation or after extended periods of inactivity.
Check out Video on Pump Priming: Click here
How to Prime a Pump
There are several methods for priming a pump, and the choice depends on the specific type of pump and the layout of the system. Let’s explore some of the most common methods:
1. Manual Priming
Manual priming is the simplest and most common way to prime a pump. This process involves directly pouring the liquid into the pump’s suction side while keeping the air vent valve open. Once the liquid begins to escape from the air vent valve, you can close the valves, and the pump is ready for operation.
2. Using an Ejector
In situations where manual priming is difficult or the pump is hard to access, an ejector can be used to prime the pump. The ejector works by creating a vacuum inside the suction line, pulling the liquid upward and into the pump. This method is useful when the pump is located above the liquid source, as it helps overcome the suction lift.
3. Installing a Foot Valve
A foot valve can be installed at the suction side of the pump. This valve prevents the liquid from draining back into the reservoir or tank when the pump is shut down. As a result, the pump remains primed for subsequent operations, eliminating the need for manual priming before each use.
4. Gravity Priming (Flooded Suction)
If the pump is situated below the liquid level in a tank or reservoir, gravity will naturally cause the liquid to flow into the pump. In such cases, the pump will always remain primed, as the liquid will continuously fill the pump chamber. This is known as a flooded suction condition and is often seen in submerged pumps or systems with elevated liquid sources.
Quiz on Consequences of Improper Pump Priming
1. What is the consequence of a pump running without liquid?
Choose the correct answer:
Correct Option: A
Explanation: Dry running occurs when a pump operates without liquid. This leads to overheating of the pump components, which can cause premature wear or even failure. For example, in centrifugal pumps, this can lead to bearing or seal damage.
2. What can cavitation inside a pump lead to?
Choose the correct answer:
Correct Option: A
Explanation: Cavitation occurs when air pockets form and collapse inside the pump, causing damage to the impeller and casing. This can severely affect the pump’s lifespan and performance. For instance, bubbles collapsing near the impeller can cause pitting and erosion.
3. What happens to pump efficiency if it’s not properly primed?
Choose the correct answer:
Correct Option: C
Explanation: Improper priming leads to reduced pump efficiency because the pump struggles to generate the required suction. As a result, it works harder, consumes more power, and performs less effectively. For example, this is common in self-priming pumps if the priming chamber is not filled properly.
4. How does improper priming affect energy consumption?
Choose the correct answer:
Correct Option: C
Explanation: A pump that is not primed correctly often consumes more energy as it has to work harder to maintain its function. This can lead to higher operational costs and strain on the motor. For example, this is especially problematic in industrial settings where pumps run for long periods.
5. What is a long-term consequence of frequent improper priming?
Choose the correct answer:
Correct Option: B
Explanation: Improper priming can lead to frequent maintenance needs because the pump components wear out faster or fail more often. For instance, seals and bearings are more likely to degrade if the pump regularly runs dry or cavitates.
Consequences of Improper Priming
Failing to prime a pump correctly can lead to a host of operational issues and long-term problems. Some of the key consequences include:
- Dry Running: If a pump operates without liquid, it is known as dry running. This can cause the pump components to overheat, leading to premature wear or even failure.
- Cavitation: When air pockets form inside the pump due to improper priming, cavitation can occur. This is the formation and collapse of vapor bubbles, which can damage the pump’s impeller and casing.
- Reduced Efficiency: Improperly primed pumps may struggle to generate the necessary suction, reducing their overall efficiency and making them work harder than they should.
- Increased Energy Consumption: A pump that is not primed correctly often consumes more energy, leading to higher operational costs.
- Frequent Maintenance: Pumps that are not regularly primed are more likely to experience failures and breakdowns, increasing the frequency of required maintenance and repairs.
Step-by-Step Guide to Manual Pump Priming
Manual priming is the most straightforward method of priming a pump. Here is a step-by-step guide to performing this task:
- Check the Pump for Air
- Ensure that the pump and the suction line are filled with air and that there are no liquid residues left from previous operations.
- Open the Air Vent Valve
- Open the air vent valve located on the pump casing. This valve will allow trapped air to escape during the priming process.
- Fill the Pump with Liquid
- Pour the liquid you plan to pump into the suction line or the pump’s priming chamber until it is full. If the liquid begins to escape from the air vent valve, close the vent valve.
- Close All Valves
- After ensuring that no more air is trapped inside the pump, close the air vent valve and any other valves used for priming.
- Start the Pump
- Once all the valves are securely closed, start the pump. It should begin drawing the liquid into the system and operate as intended.
Pump Priming Methods at a Glance
Method | Description | Ideal For |
---|---|---|
Manual Priming | Pour liquid into the pump manually, open air vent valve, and wait for liquid to escape | Simple systems and easily accessible pumps |
Ejector Priming | Use a vacuum device to pull liquid into the suction line | Pumps located above the liquid source |
Foot Valve Priming | Install a valve to prevent liquid from draining out of the pump | Systems that need to maintain prime between uses |
Gravity Priming | Utilize a liquid source above the pump to create a natural flow into the pump | Submerged or gravity-fed systems |
Common Mistakes in Pump Priming
Even though pump priming seems like a straightforward task, there are common mistakes that operators should avoid to ensure optimal pump performance.
1. Skipping the Air Vent Valve
Always open the air vent valve when priming a pump. Failing to do so may leave air trapped inside, which can lead to airlock and inefficient pump operation.
2. Not Checking the Suction Line
Before priming, make sure that the suction line is properly connected and free from leaks. A loose connection can allow air to enter, disrupting the priming process.
3. Rushing the Process
Priming takes time. Ensure that the pump is completely filled with liquid before closing the air vent valve. Prematurely closing the valve can result in incomplete priming.
Pump Priming in Different Industries
Pump priming is essential in various industries, and the process may differ based on the type of pump and application. Let’s explore how pump priming plays a role in different sectors:
1. Water Treatment
Water treatment plants rely heavily on pumps to move water through the purification process. Regular priming is required to ensure that the pumps do not experience airlock or cavitation, which could interrupt water flow.
2. Oil and Gas
In the oil and gas industry, pumps are used to transport crude oil and refined products. Proper priming is crucial to avoid air pockets, which could cause cavitation and damage to the pump’s internal components.
3. Chemical Processing
Chemical processing plants use pumps to move liquids through various stages of production. Given the sensitive nature of many chemicals, priming is critical to maintaining safe and efficient operation.
4. Agriculture
Irrigation systems rely on pumps to transport water to crops. Priming ensures that these pumps operate reliably, preventing dry running that could harm crops during peak growing seasons.
FAQs About Pump Priming
- What is pump priming? Pump priming is the process of removing air from a pump and its suction line by filling it with the liquid that needs to be pumped, ensuring that the pump can create enough suction to operate effectively.
- Why is pump priming important? Pump priming is crucial because it prevents airlock, dry running, and cavitation, all of which can damage the pump and reduce its efficiency.
- Do all pumps require priming? No, not all pumps require priming. Centrifugal pumps generally need priming, while self-priming and submerged pumps may not.
- What are the consequences of failing to prime a pump? Failing to prime a pump can lead to airlock, dry running, cavitation, and inefficient operation, all of which can cause significant damage to the pump.
- What is the easiest method to prime a pump? Manual priming is the simplest method, involving filling the pump with liquid through the suction side and opening the air vent valve until all trapped air is released.
Popular courses by EPCLAND on Piping Engineering:
- Complete Course on Piping Engineering
- Piping Layout Engineering
- Piping Material Engineering
- Piping Stress Analysis
- All Courses Published on EPCLAND Platform
Top Short Courses on valves by EPCLAND:
- 14 Components of API 6A Gate Valve
- 14 Components of API 6D Valves
- 58 Components of API 602 Gate Valves
- 17 Components of API 600 Gate Valves
- Valve Material Specifications (VMS) – Comprehensive Guide
Important Links
- Video Series on Comparison of Piping Items: Check here
- Join Biggest Telegram Community of Piping Engineering: Click Here
- Subscribe YouTube channel: Click Here
- Check All Published courses: Click Here
- Read published technical Articles: Click Here
#Epcland #Pipingcourses #PIpingengineering #pipingonlinecourses #atulsingla